Line 58: | Line 58: | ||
</div> | </div> | ||
<div class="col-md-3"> | <div class="col-md-3"> | ||
− | <a href="# | + | <a href="#electronics" class="darkBlue" style="font-family: 'Pacifico'"><h2 style="text-align: center">Electronics Assembly</h3></a> |
</div> | </div> | ||
<div class="col-md-3"> | <div class="col-md-3"> | ||
Line 226: | Line 226: | ||
</section> | </section> | ||
− | <section id=" | + | <section id="electronics" style="background-color:#fff; text-align: center"> |
<div class="container" style:"padding:0% 0% ; margin:0% 0%"> | <div class="container" style:"padding:0% 0% ; margin:0% 0%"> | ||
− | <h2 style="font-family:Pacifico ; text-align: center"> | + | <h2 style="font-family:Pacifico ; text-align: center">Electronics Assembly</h2> |
− | <p style="font-family:'Roboto Condensed'; font-size:150%">1. | + | <p style="font-family:'Roboto Condensed'; font-size:150%">1. Clamp DIN rail in a vice and cut to fit inside the electronics box using a hacksaw (160mm will fit nicely inside the 220 mm x 220 mm x 100 mm box template given in this protocol).</p> |
− | <p style="font-family:'Roboto Condensed'; font-size:150%"> | + | <p style="font-family:'Roboto Condensed'; font-size:150%">2. Slide the relay and the terminal connectors onto the DIN rail (two are for use as spacers between the relay and the other three terminals for mains connections) and place inside the box (figure 1)</p> |
− | < | + | <p style="font-family:'Roboto Condensed'; font-size:150%">For the following steps, wire up the circuit according to the circuit diagram given on page 4 (figure 15). Take note of the wire colour-coding convention and different wire thicknesses used.</p> |
− | + | <p style="font-family:'Roboto Condensed'; font-size:150%">3. Strip 5 cm of outer black insulation from each end of the curly cord mains cable, then strip 1-2cm of coloured insulation from each of the cable’s inner wires.</p> | |
− | </ | + | <p style="font-family:'Roboto Condensed'; font-size:150%">4. On one end of the mains cable, thread each of the inner wires into a crimp terminal until all the exposed wire and 2-3 mm of insulation is inside the terminal. Using the crimping tool, crimp the wire and terminal together - make sure the exposed wire does not slip out as you crimp it.</p> |
− | + | <p style="font-family:'Roboto Condensed'; font-size:150%">5. Slide each crimp terminal onto the appropriate male connection of the IEC filter (figure 2).</p> | |
+ | <p style="font-family:'Roboto Condensed'; font-size:150%">6. Insert two 3A fuses into the fuse cartridge holder of the IEC (figure 3). Attach the IEC filter to the inside of panel with the 60x30 mm rectangular cutout using the two M3 screws and nuts.</p> | ||
+ | <p style="font-family:'Roboto Condensed'; font-size:150%">7. Secure the exposed wires on the other end of the curly cable into one side of the appropriate DIN rail screw terminal block (figure 4).</p> | ||
+ | <p style="font-family:'Roboto Condensed'; font-size:150%">8. Place the 24V SMPS inside the box - use the layout of components in the box as a guide of how long to cut the circuit wires (bear in mind you will need to strip at least 1 cm of insulation from each end of each wire).</p> | ||
+ | <p style="font-family:'Roboto Condensed'; font-size:150%">9. Cut the appropriate lengths of the wires shown in the circuit diagram, and strip 1 cm of insulation from each end. The number of wires and approximate lengths once trimmed to fit in the box are given in table 1 below.</p> | ||
<TABLE style="font-family:Arvo; font-size:130%; border: 5px;margin-left:auto; margin-right:auto"> | <TABLE style="font-family:Arvo; font-size:130%; border: 5px;margin-left:auto; margin-right:auto"> | ||
<TR> | <TR> | ||
− | <TH><b> | + | <TH><b>Wire</b></TH> |
− | <TH><b> | + | <TH><b>Quantity</b></TH> |
+ | <TH><b>Approximate length(s)/ mm</b></TH> | ||
</TR> | </TR> | ||
<TR> | <TR> | ||
− | <TD> | + | <TD>16/0.2 mm brown</TD> |
− | <TD> | + | <TD>2</TD> |
+ | <TD>16/0.2 mm brown</TD> | ||
</TR> | </TR> | ||
<TR> | <TR> | ||
− | <TD> | + | <TD>16/0.2 mm red</TD> |
− | <TD> | + | <TD>3</TD> |
+ | <TD>150, 140, 1000</TD> | ||
</TR> | </TR> | ||
<TR> | <TR> | ||
− | <TD> | + | <TD>16/0.2 mm yellow-green</TD> |
− | <TD> | + | <TD>2</TD> |
+ | <TD>1000, 100</TD> | ||
</TR> | </TR> | ||
<TR> | <TR> | ||
− | <TD> | + | <TD>7/0.2 mm blue</TD> |
− | <TD> | + | <TD>2</TD> |
+ | <TD>100, 1000</TD> | ||
</TR> | </TR> | ||
<TR> | <TR> | ||
− | <TD> | + | <TD>16/0.2 mm black</TD> |
− | + | <TD>1</TD> | |
− | + | <TD>100</TD> | |
− | + | ||
− | <TD>1 | + | |
− | <TD> | + | |
</TR> | </TR> | ||
</TABLE> | </TABLE> | ||
− | |||
− | |||
− | |||
− | |||
− | |||
− | |||
− | |||
− | |||
− | |||
− | |||
− | |||
<p style="font-family:'Roboto Condensed'; font-size:150%">10. Open the outlet valve very slightly and make sure it is directed away from you and anyone surrounding the gun.</p> | <p style="font-family:'Roboto Condensed'; font-size:150%">10. Open the outlet valve very slightly and make sure it is directed away from you and anyone surrounding the gun.</p> | ||
<p style="font-family:'Roboto Condensed'; font-size:150%">11. <b>Very gently</b>, open the CO2 pump handle as little as possible. If the pressure rises above 10 bar very quickly, turn off the CO2 supply then close the outlet valve. Briefly open and close the outlet valve until the pressure falls below 10 bar, to your desired firing pressure (recommended 100-140 psi).</p> | <p style="font-family:'Roboto Condensed'; font-size:150%">11. <b>Very gently</b>, open the CO2 pump handle as little as possible. If the pressure rises above 10 bar very quickly, turn off the CO2 supply then close the outlet valve. Briefly open and close the outlet valve until the pressure falls below 10 bar, to your desired firing pressure (recommended 100-140 psi).</p> |
Revision as of 22:58, 17 October 2016
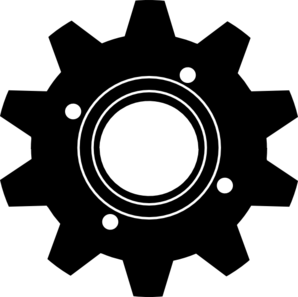
£236.40
OUR LOW-COST, OPEN SOURCE GENE GUN: DEMOCRATISING THE TECHNOLOGY FOR CHLOROPLAST ENGINEERING
Gun Assembly
1. Following the method shown in the video below, apply PTFE tape to all BSPT threads - see table 1 for a list of the relevant hardware parts. I wrapped the threads 6-8 times, which seems more than sufficient.
Note: each time you unscrew a taped thread from the gun once it is assembled, you will need to remove the old tape and reapply following the method above before reattaching it.
Part name | Side(s) to apply PTFE tape to |
---|---|
Schrader valve | ⅛” BSPT male |
1/4" to 1/8" reducer< | 1/4” BSPT male |
Pressure gauge | ¼” male G thread |
1/4” male-male coupler (quantity = 2) | Both sides |
Needle valve | Both sides |
1/2” to 1/4” reducer | Both sides |
2. Connect parts together for the upper half of the gun according to the diagram given in figure 1, and tighten the connections by hand.
3. Clamp the half gun in the vice and use the adjustable spanner to tighten each part until there is too much resistance to further tighten the connection. Note: do not overtighten the schrader-⅛” BSPT to ¼”-⅛” reducer connection (figure 2).
4. Unscrew the outer cartridge case on the CO2 pump (figure 3), and screw in a 16g threaded CO2 cartridge tightly.
5. UNDERWATER PRESSURE TEST (figure 4 - previous design shown) Fill your bucket with enough water to fully submerge the gun. Put the gun underwater, with the needle valve closed, and carefully open the pump as little as possible (the gas will come out very quickly when using a new cartridge). If the gun’s connections are sealed, you should only see bubbles come out the exposed end of the female tee. Try opening the needle valve after this, to check the outlet valve flow by observing bubbles coming out of the outlet.
Troubleshooting: if there are leaks in the gun, try tightening the connections again more thoroughly in the vice. Alternatively, check the connections are screwed in straight - if the ends are taped unevenly, the joints will be at a slight angle and will not be sealed properly. In this case, undo the connections, remove the old PTFE tape and re-tape the ends, taking care to wrap the tape evenly. Put the connections back together and then try pressure testing again.
6. Connect up the lower half of the gun, excluding the nozzle (refer to figure 1 again), and tighten using the adjustable spanner and vice as before.
7. Position the base onto the clamp stand and attach the clamps.
8. Clamp the gun to the stand - suggested positions for clamping are shown in figure 5. Adjust the height of the gun so its open end is approximately 5-8 cm from the stand base for initial testing.
9. Test firing without nozzle (I would recommend labelling the directions for the outlet valve as shown in figure 6, as a reminder when it needs to be closed quickly): If you are using a fresh cartridge of CO2, proceed carefully - the gun requires practice to fine tune reaching a desired pressure, and will be very sensitive at first. Wear eye protection and make sure the safety shield is in place around the gun (figure 7).
10. Open the outlet valve very slightly and make sure it is directed away from you and anyone surrounding the gun.
11. Very gently, open the CO2 pump handle as little as possible. If the pressure rises above 10 bar very quickly, turn off the CO2 supply then close the outlet valve. Briefly open and close the outlet valve until the pressure falls below 10 bar, to your desired firing pressure (recommended 100-140 psi).
12. If the pressure increases slowly (if you are using a half-empty cartridge, for example), you can close the outlet valve and keep the CO2 supply open until it reaches your desired pressure (still below 10 bar), then switch off the CO2 supply.
13. Ensure all hands/appendages are clear of the open end of the gun. Then, switch on the electrical box at mains and at the IEC filter (check the green SMPS LED illuminates at this point.
When you are ready to fire, depress the red trigger switch - there should be a fairly loud pop!
If the gun does not fire properly, you can release any remaining CO2 from the gun using the outlet valve - ensure this is also clear of bodily appendages before opening.
14. Nozzle composition (figure 8) - remove the rubber o-ring inside the nozzle, insert mesh filter into the hose nozzle, then reinsert the rubber o-ring on top. Cut a 5x3 cm piece of parafilm and place taught between two washers (figure 9). Trim the edges around the washers slightly, then fold any remaining parafilm over the sides of the washer and flatten (figure 10). Place the washer-parafilm sandwich on top of the mesh filter, then top with the o-ring in the nozzle (figure 11).
15. Rupture disc testing - repeat steps 10-12, then screw the nozzle onto the gun firmly in place (video clip 1). Make sure the safety guard is in place, then depress the red trigger switch on the electronics box. You should hear a loud pop of the parafilm rupturing.
16. Inspect the uniformity of the ruptured parafilm by unscrewing the nozzle (figure 12).
17. You can then experiment with thickness of parafilm (by stretching before sandwiching between the washers) and firing pressure, repeating steps 15 & 16 to optimise these parameters.













Electronics Assembly
1. Clamp DIN rail in a vice and cut to fit inside the electronics box using a hacksaw (160mm will fit nicely inside the 220 mm x 220 mm x 100 mm box template given in this protocol).
2. Slide the relay and the terminal connectors onto the DIN rail (two are for use as spacers between the relay and the other three terminals for mains connections) and place inside the box (figure 1)
For the following steps, wire up the circuit according to the circuit diagram given on page 4 (figure 15). Take note of the wire colour-coding convention and different wire thicknesses used.
3. Strip 5 cm of outer black insulation from each end of the curly cord mains cable, then strip 1-2cm of coloured insulation from each of the cable’s inner wires.
4. On one end of the mains cable, thread each of the inner wires into a crimp terminal until all the exposed wire and 2-3 mm of insulation is inside the terminal. Using the crimping tool, crimp the wire and terminal together - make sure the exposed wire does not slip out as you crimp it.
5. Slide each crimp terminal onto the appropriate male connection of the IEC filter (figure 2).
6. Insert two 3A fuses into the fuse cartridge holder of the IEC (figure 3). Attach the IEC filter to the inside of panel with the 60x30 mm rectangular cutout using the two M3 screws and nuts.
7. Secure the exposed wires on the other end of the curly cable into one side of the appropriate DIN rail screw terminal block (figure 4).
8. Place the 24V SMPS inside the box - use the layout of components in the box as a guide of how long to cut the circuit wires (bear in mind you will need to strip at least 1 cm of insulation from each end of each wire).
9. Cut the appropriate lengths of the wires shown in the circuit diagram, and strip 1 cm of insulation from each end. The number of wires and approximate lengths once trimmed to fit in the box are given in table 1 below.
Wire | Quantity | Approximate length(s)/ mm |
---|---|---|
16/0.2 mm brown | 2 | 16/0.2 mm brown |
16/0.2 mm red | 3 | 150, 140, 1000 |
16/0.2 mm yellow-green | 2 | 1000, 100 |
7/0.2 mm blue | 2 | 100, 1000 |
16/0.2 mm black | 1 | 100 |
10. Open the outlet valve very slightly and make sure it is directed away from you and anyone surrounding the gun.
11. Very gently, open the CO2 pump handle as little as possible. If the pressure rises above 10 bar very quickly, turn off the CO2 supply then close the outlet valve. Briefly open and close the outlet valve until the pressure falls below 10 bar, to your desired firing pressure (recommended 100-140 psi).
12. If the pressure increases slowly (if you are using a half-empty cartridge, for example), you can close the outlet valve and keep the CO2 supply open until it reaches your desired pressure (still below 10 bar), then switch off the CO2 supply.
13. Ensure all hands/appendages are clear of the open end of the gun. Then, switch on the electrical box at mains and at the IEC filter (check the green SMPS LED illuminates at this point.
When you are ready to fire, depress the red trigger switch - there should be a fairly loud pop!
If the gun does not fire properly, you can release any remaining CO2 from the gun using the outlet valve - ensure this is also clear of bodily appendages before opening.
14. Nozzle composition (figure 8) - remove the rubber o-ring inside the nozzle, insert mesh filter into the hose nozzle, then reinsert the rubber o-ring on top. Cut a 5x3 cm piece of parafilm and place taught between two washers (figure 9). Trim the edges around the washers slightly, then fold any remaining parafilm over the sides of the washer and flatten (figure 10). Place the washer-parafilm sandwich on top of the mesh filter, then top with the o-ring in the nozzle (figure 11).
15. Rupture disc testing - repeat steps 10-12, then screw the nozzle onto the gun firmly in place (video clip 1). Make sure the safety guard is in place, then depress the red trigger switch on the electronics box. You should hear a loud pop of the parafilm rupturing.
16. Inspect the uniformity of the ruptured parafilm by unscrewing the nozzle (figure 12).
17. You can then experiment with thickness of parafilm (by stretching before sandwiching between the washers) and firing pressure, repeating steps 15 & 16 to optimise these parameters.













Bio-Makespace
Biomakespace is an initiative of synthetic biology scientists, students and enthusiasts in Cambridge who are working hard to build a new community laboratory. We aim to have a friendly sharing space where scientists could meet engineers, physicists, computer scientists, medics and other professionals but even public, students and schools. They all could start working together on synthetic biology projects from this academic year already. The iGEM team got involved with establishing of the space, planning and propagation from the very beginning.
A few of us are planning to share with other students what we have learned from synthetic biology over the summer by leading or participating projects based on cell-free systems there in the coming academic year under the flag of the new student-led Cambridge University Synthetic Biology Society
Emerging Biomakespace and similar community labs have also hugely motivated us for our hardware sub-projects as Biomakespace hasn’t initially considered working on plants and algae or their chloroplasts much. By offering our affordable hardware to them and similar community labs over the world we will facilitate further development of plant and algal synthetic biology and also work on chloroplasts. As an example biolistics is the only reliable way to transform chloroplasts of plants or algae. However costs of commercial gene guns are absolutely beyond what such labs can usually afford. We are offering a cheap and tested alternative opening a whole new range of possible projects for them.
Official aims of Biomakespace:
- Bring together biologists, engineers, technologists and others in the Cambridge area for meeting, co-working and socialising in a creative, cross-disciplinary, community-driven and safe environment.
- Provide a well-equipped space for practical biology and engineering of biology on a community membership basis.
- Support new and existing interdisciplinary collaborations for engineering biology, with a focus on promoting open technology and innovation.
- Raise awareness, understanding and participation in biology and engineering of biology in the Cambridge area through public engagement activities, education and training.
- Foster links with local industry and innovation organisations, building bridges between academia and bioenterprise.